The process started by watching videos and learning the basics of 3D modelling using two different workflows: 3D sculpting and technical design. This was mainly done on the softwares like Blender, Fusion 360. It taught how to set up 3D objects to create beautifully lit and creatively composed renders.
The next step was to learn how to 3D scan small and large objects using photogrammetry, which uses only images taken from various angles to create a 3D model. During the course, various objects including interiors and exteriors of buildings, furniture and artefacts, a human body, etc were scanned along with learning the technical aspects of working with 3D meshes. Learning to process these models and to manipulate them and build over them was the main aim. Introduction to using models in digital simulations, videos or games was a part of the process.
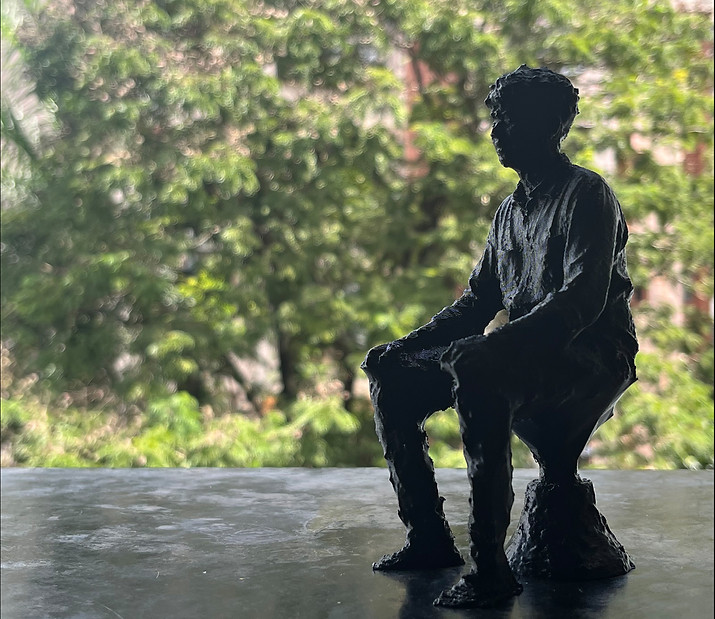
Photogrammetry- Scanning a human body from all the angles in a circular manner and generating a 3D model from the images and finally 3D printing it.
In pursuit of a kinetic piece of art, jewellery designing was explored, creating unique wearable expressions using materials, forms, and techniques. Specialized software tools enabled precise visualization and dynamic movement, resulting in meaningful pieces of kinetic jewellery.

Form follow Fabric
In collaboration with Jay Kanti
The final part of the project intended to take up a project in a group of two about something that interests oneself. For this, drawing inspiration from previous experiments involving cloth and stitching techniques, the primary objective of the project was to explore the dynamic potential of prestressed fabric when combined with various 3D printed patterns.
​
By integrating cutting-edge software tools like Fusion 360, Blender, Prusa Slicer, and Chitubox, an effort was made to create a harmonious fusion of technology and textiles, giving rise to innovative and visually captivating objects.
​
Initially, exploration using Fevigel and a 3D printing pen, allowing rapid prototyping and iteration. We experimented with an array of organic patterns, intricate grids, and varied shapes, among other possibilities.
Ex 1. Aim: To experiment on small patches of stretched tensile fabric with feviquick gel as stiffener for drawing patterns in order to get the quick results.
Observation: (1) Grid pattern on stretched fabric resulted in undulating surfaces at intersections upon release. (2) Circular stiffened areas flatten while the remaining fabric drapes around them giving an overall form to the fabric.
Ex 2. Aim: To experiment on small patches of stretched fabric with 3D printing pen as stiffener for drawing patterns in order to understand how the material (PLA) works on fabric.
Observation: (1) The circular stiffened areas took form because of the force of fabric while the remaining fabric drapes around it. (2)Cross grid pattern caused bulging mount-like peaks at intersections.
Ex 3. Aim: To experiment with grid patterns on stretched tensile fabric over a metal plate of a 3d printer .
Observation: (1) Grid pattern on stretched fabric resulted in undulating surfaces at intersections upon release.
Ex 4. Aim: To experiment with organic contoured patterns on stretched tensile fabric over a metal plate of a 3d printer .
Observation: (1) Grid pattern on stretched fabric resulted in undulating surfaces at intersections upon release.
Ex 5. Aim: After numerous iterations, we identified a singular shape that resonated strongly with our vision. This chosen shape was then 3D printed in various sizes and thicknesses, further amplifying its versatility.
Result: By ingeniously stitching together multiple reproductions of the printed shape, we crafted a garment that pushed the boundaries of both fashion and art.
The project “Form follows fabric” embodies the seamless integration of artistry and technology, showcasing the results achieved by marrying prestressed fabric with 3D printed patterns. By constantly pushing creative boundaries, we aspire to redefine traditional design paradigms and inspire innovative applications across disciplines.
The video demonstrates the entire process carried out during the course period.